Want to Subscribe?
Read Corporate India and add to your Business Intelligence
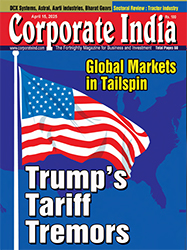
Unlock Unlimited Access
Published: September 15, 2024
Updated: September 15, 2024
With the Indian automobile industry growing by leaps and bounds on the back of a booming economy, better road infrastructure and growing consumer demand, tyres -- an essential automobile component - are also seeing their day in the sun.
Another Another Another important tyre 'driver' is the Indian government's focus on road infrastructure, which has led to an increase in vehicle sales and has subsequently boosted the demand for tyres. Besides, the growing demand for luxury cars has led to a market for premium tyres.
The latest kid on the block is OTR (off-theroad) tyres, which deliver optimal performance for vehicles engaged in 'heavy lifting'. And the growing yen for tyres is not just domestic. Indian tyres are today in great demand globally, with the US alone accounting for nearly 25 per cent of Indian tyre exports.
According According to one industry report, the Indian tyre industry is currently worth $ 13.11 billion and is projected to reach a whopping $ 25.50 billion by 2031. Corporate India brings its readers a curated list of 5 top automotive tyre stocks.
The $ 14.25 billion Indian tyre industry has shifted into high gear. The industry, which has on average been turning out 200 million tyres every year, has started growing at a CAGR of 8.71 per cent. Experts have projected the size of the industry to reach $ 25.50 billion by 2031, mainly owing to the rapidly growing automobile industry in the country.
Tyres have emerged as an essential component of the automotive ecosystem, as they play a crucial role in ensuring vehicle safety and performance. In recent years, the automotive market has witnessed several key drivers that have propelled its growth. Rising disposable incomes, a growing high middle-class population, a spurt in the young population and a better standard of living have directly translated into increased demand for automobiles and, in turn, for tyres. Additionally, government initiatives such as ‘Make in India’ and the push for electric vehicles have further contributed to the market’s growth.
Another important driver for automotive growth is the focus on road infrastructure development. The Indian government has been investing heavily in building highways and other new roads for better transportation connectivity, which has led to an increase in vehicle sales and subsequently boosted the demand for tyres.
As an expert notes, a better road infrastructure has positively impacted the market for luxury cars in India. In fact, more than 16,000 luxury vehicles were sold in India in the first six months of 2022 and the demand continues unabated. Little wonder that in 2023, JK Tyres launched a premium tyre brand, ‘Levitas Ultra’, in order to meet the ever-growing demand for luxury cars.
For the last three years, the country has witnessed not only a marked increase in demand for passenger vehicles and their tyres but, of late, also an increased demand for OTR (off-the-road) tyres. The main drivers for the spurt in demand for OTR tyres include: (1) Significant infrastructure development in the country, including the construction of roads, highways and airports. These projects require heavy machinery and vehicles that rely on OTR tyres for optimal performance in challenging terrains; (2) Substantial growth in the mining and construction sectors. OTR tyres are essential for heavy duty vehicles used in mining operations, earthmoving equipment and construction projects; and (3) The agriculture sector, which heavily relies on tractors and other agriculture machinery. The expansion of mechanised farming practices and the need for increased productivity have driven the demand for reliable and durable OTR tyres.
Overall, the increase in infrastructure development growth in the mining and construction sectors, and the mechanisation of agriculture, have all fuelled the demand for OTR tyres in the Indian tyre market. Manufacturers have responded by expanding their OTR tyre offerings in order to meet this demand. For example, BKT Tyres is creating India- centric products, whether it is Mine Force for the mining sector, the Commander series for the agriculture sector, or the soon-to-be launched addition to the Earthmover series.
In recent years, the Indian tyre market has witnessed a shift towards a greener approach in tyre manufacturing. Several key players in the industry are actively adopting sustainable practices to reduce their environmental footprint. This includes the development and production of ecofriendly tyres that promote fuel efficiency and reduce carbon emissions. Manufacturers are increasingly focusing on incorporating sustainable materials, such as bio-based and recycled materials, in tyre production. They are also investing in R&D to improve tyre design and tread patterns, resulting in reduced rolling resistance and improved fuel efficiency.
Furthermore, tyre manufacturers are implementing energy-efficient manufacturing processes and adopting measures to reduce waste generation and enhance recycling and disposal. Government initiatives promoting sustainability and environmental conservation are also driving this green approach in the Indian tyre market.
With increasing consumer awareness and demand for eco-friendly products, tyre manufacturers are embracing sustainable practices to meet the evolving market needs and contribute to greener future. For instance, Ceat Tyres, a leading tyre company belonging to Harsh Goenka, introduced the Ceat ‘Fuel Smart’ range of tyres a couple of years ago, designed to promote fuel efficiency and reduce carbon emissions. The Fuel Smart range utilises innovative tread compounds and advanced tread patterns to minimise rolling resistance, resulting in improved mileage and lower fuel consumption.
Recently, Prime Ministry Narendra Modi urged the industry to work with farms and reduce the import of rubber. According to Arnab Banerjee, chairman of the Automotive Tyre Manufacturers Association (ATMA), the industry consumes around 13 lakh tonnes of natural rubber, while India produces only 8 lakh tonnes. Four major tyre makers represented by ATMA have committed Rs 1,100 crore for rubber plantations on a total of 2 lakh hectares in the North Eastern states so as to increase domestic production.
The primary drivers are rising demand for vehicles and a sharp focus on -- and continuous government investments in --infrastructure. Additionally, a large and growing population of vehicles will continue to support tyre demand in the replacement market.
India is among the leading tyre manufacturers globally. Apart from conventional radial and bias tyres, the industry offers advanced, smart, noise-reduction, puncture-proof and electric vehicle versions. It is also expanding its presence in the premium and luxury tyre segments, which are dominated by imports.
The study estimates that the industry's turnover will increase a solid 100 basis points to 3.4% of India's manufacturing gross domestic product (GDP) by fiscal 2032, compared with 2.2% in fiscal 2022. Further, its contribution to Goods and Services Tax (GST) will rise to $ 4.1 billion from $ 2 billion, the number of jobs supported to 3.7 million from 1.9 million, and its share in global trade to 4.5% from 3.1%
The research and development (R&D) expenditure of the industry is forecast to more than double to $ 151 million from $ 64 million, after growing threefold in the past five fiscals.
Says Mr Banerjee, "The Indian tyre industry has the potential to lead domestic manufacturing on the global stage. This could be India's moment if we are able to seize the opportunity offered by the 'China + 1' policy by promoting sectors such as tyre manufacturing, which has proven its credentials. Today, India has some of the finest radial tyre manufacturing facilities in the world and the products are world-class, as is evident from the rising demand for them worldwide. India-manufactured tyres are being exported to more than 170 countries, with the US and Europe buying the most. It is time the industry is empowered in terms of raw material security and by pulling down barriers affecting exports.
A notable aspect of the rising demand for tyres of late is the spurt in demand for the electrical vehicle (EV) market. In view of the government's push for the EV segment -- if the government plans are any guide -- by 2025 the Indian EV market is expected to reach $ 7.09 billion. The government's vision for electric vehicle charging infrastructure will further boost the demand for electric vehicles in India. India is the third biggest automobile market in the world, the biggest producer of tractors, three-wheelers and passenger cars, and the second biggest producer of twowheelers. Last year, India produced 5.8 million automobiles in total, which also increased the marketshare of tyres in India. As the average age of vehicles on Indian roads increases, there is a growing demand for replacement tyres. This has been driven by the increasing awareness of the importance of tyre maintenance and safety.
Furthermore, India's EV finance sector is expected to grow to $ 50 billion by 2030, as per NITI Aayog and the Rocky Mountain Institute (RMI). According to industry reports, the EV market in India will increase at a CAGR of 36% until 2026. Along with companies exploring the rural markets, greater demand for logistics and passenger transportation has collectively boosted the India tyre market's opportunities.
Along with the sustained domestic demand for tyres, there has been an upswing in overseas demand for Indian tyres. The Indian tyre industry has started very well on the export front. Today, Indian tyres are plying in over 170 countries, with large demand coming from the EU, the US, Brazil, the UAE, and the UK. Today, the US is the largest market for Indian tyres, accounting for nearly 25 per cent of the total tyre exports from India.
The tyre makers' association is also pushing the government for free trade agreements with Latin American and African countries so as to boost earnings to the tune of Rs 23,400 crore. According to Mr Singhania, exports from India are seeing promising markets in Western countries. He notes, "If trends in the export demand for Indian tyres at present are any indication, I am confident that our exports will double to around Rs 50,000 crore by the end of the decade, i.e., by 2030."
According to Mr Singhania, "Earlier, our export portfolio did not fully cater to the demands of global markets. But now there has been a significant investment in TBR, PCR and off-highway tyres, and this will drive the demand going forward. Also, many of our standards are now aligned with the rest of the world, which will be a supportive factor in accelerating exports."
All said and done, the prospects for the Indian tyre industry are highly promising. The Indian automotive market size, which was valued at $ 101.8 billion in 2023, is expected to grow to around $ 218 billion by 2031. This means that the Indian tyre industry will also record robust growth, going ahead.
According to a comprehensive report on the Indian tyre industry by Markets and Data, the Indian tyre industry is projected to reach from $ 13.11 billion in 2023 to $ 25.50 billion by 2031. Significantly, the Indian tyre industry has not only sufficient tyre manufacturing capacity to take care of domestic demand as well as rising export demand, but is also planning to expand its capacity to take care of future demand.
There are 41 tyre companies in India. We have selected the top five companies which should be on the radar of discerning investors. Here goes the list.
MRF Ltd, the costliest stock on the Indian stock exchanges, is a dominant player in the Indian tyre manufacturing industry. Formerly known as Madras Rubber Factory, the company is renowned for its exceptional financial performance, strong market presence and robust brand equity. Headquartered in Chennai, the company's product segment is divided into tyres, sports goods, funskool, paints & coats, and pretreads.
In the tyre segment, MRF offers tyres for a wide range of categories, such as heavy-duty trucks and buses, light trucks, multi-utility vehicles (MUVs), recreational vehicles (RCVs) and passenger cars. Additionally, it provides tyres for motorsports, agricultural or farm use, military applications, forklifts, two-wheelers, three-wheelers, and off-road vehicles or earthmovers. The company provides tyres for different models of various renowned vehicle brands like Toyota, Volvo, Nissan, Ford, Audi, Hyundai, BMW, Volkswagen, Mahindra and Maruti. Moreover, MRF Limited provides services like tyre changing, tyre repair, tyre maintenance, wheel balancing, robotic wheel alignment, nitrogen filling and automatic car wash.
Investors and market analysts are constantly intrigued by the unbelievable high price of MRF stocks which trade at an exorbitant premium compared to peers in the industry. The company has a track record of consistent financial performance, characterised by steady revenue growth, healthy profit margins and strong return on equity (ROE). During the last 12 years, the company's sales turnover has steadily expanded from Rs 11,964 crore in the financial year ended September 2012 to Rs 25,169 crore in fiscal year 2024, with operating profit more than trebling from Rs 1,272 crore to Rs 4,272 crore and the profit at net level shooting up more than four times from Rs 579 crore to Rs 2,081 crore.
The company's financial position is unbelievably strong, with reserves at the end of 2024 standing at Rs 16,699 crore - almost 4,175 times its tiny capital of Rs 4 crore.
An undisputed global leader in the off-highway tyre industry for over three decades, Balkrishna Industries Limited, popularly known as BKT, leads in designing and manufacturing safe, innovative and high-performing tyres for various industries like construction, agriculture, mining, earthmoving and ports. The company also manufactures tubes and carbon black. Its main products include off-the-road tyres, agricultural tyres and industrial tyres. The company's agricultural tyres are used for various applications, including tractors, harvesters, agro trucks and telehandlers. Its industrial tyres serve applications such as forklifts, excavators, container handlers, compactors and mobile cranes.
Additionally, BKT's off-the-road tyres are used for rigid dump trucks, articulated dump trucks, scrapers, underground mining vehicles, etc. Moreover, BKT serves both original equipment manufacturers (OEMs) and the replacement market. With 4 manufacturing plants located in Maharashtra, Rajasthan and Gujarat, BKT distributes its products through third-party distributors and exports them worldwide. BKT also has distribution partners in over 160 countries across 5 continents, allowing it to serve a truly global customer base. The company has made rapid strides on the financial front. During the last 12 years, its sales turnover has almost trebled from Rs 3,390 crore in fiscal year 2013 to Rs 2,256 crore in fiscal 2024, with operating profit shooting up almost four times - from Rs 669 crore to Rs 2,256 crore and the net profit spurting to Rs 1471 crore. The company's financial position is extremely strong, with reserves as on March 31, 2024 standing at Rs 8,815 crore - 200 times its equity capital of Rs 39 crore.
Driven by innovation, Gurgaon-based Apollo Tyres Ltd is an international tyre manufacturer and the leading tyre brand in India. It is built around the core principles of creating stakeholder value through reliability in its products and de-
pendability in its relationships. The company has a total of six manufacturing units -- 4 in India and 1 each in the Netherlands and Hungary. India's fifth and 7th globally, its plant is coming up in Andhra Pradesh. Besides the organic route, the company has also grown through the inorganic route. In November 2015, Apollo Tyres acquired Reifencom GmbH, one of the largest tyre distributors in Germany, with both an online and offline presence. In May 2009, the company acquired Apollo Vredestein BV (originally Vredestein Banden BV) in the Netherlands, producer of niche highend passenger car and speciality tyres, which has an extensive distribution network across Europe.
The company markets its products under its two global brands -Apollo and Vredestein -- and its products are available in over 100 countries through a vast network of branded, exclusive and multi-product outlets. The product portfolio of the company includes the entire range of passenger car, SUV, MUV, light truck, truck-bus, two-wheeler, agriculture, industrial, speciality, bicycle and off-the-road tyres, and retreading material and tyres. Headquartered in Gurgaon, India, the company has a turnover of $ 2.3 billion and ranks among the global top 20 tyre makers. Apollo Tyres has been recognised as the 'Best Company To Work For' both in Asia and Europe in the recent past, and has won several accolades for its HIV-AIDS awareness and prevention initiative for the trucking and allied communities, and for its Waste Management initiatives in the community.
The company has steadily grown in its financial performance. During the last 12 years, its sales turnover has more than doubled from Rs 12,799 crore in fiscal 2013 to Rs 25,378 crore in fiscal 2024, with operating profit more than trebling from Rs 1,471 crore to Rs 4,468 crore and the net profit almost trebling from Rs 612 crore to Rs 1,722 crore. The company's financial position is sound, with reserves at the end of March 2024 standing at Rs 13,839 crore, over 200 times its equity capital of Rs 64 crore.
JK Tyre & Industries Limited, a leading tyre manufacturer belonging to the Singhania group, offers comprehensive solutions for various vehicle segments. The company provides passenger car tyres, commercial tyres, farm tyres, two-wheeler tyres, three-wheeler tyres and off-the-road tyres. The company also provides puncture guards to prevent punctures. JK Tyre introduced India's first-ever 'Smart Tyre' technology, featuring Tyre Pressure Monitoring Systems (TPMS) with TREEL sensors that monitor crucial tyre statistics like pressure and temperature. The company and its subsidiaries develop, manufacture, market and distribute automotive tyres, tubes, flaps, and retreads. JK Tyre primarily operates in multiple segments, including India and Mexico, with a notable presence in 105 countries through over 180 global distributors. With a network of over 4,000 dealers and more than 500 brand shops named Xpress Wheels, Truck Wheels and Steel Wheels, JK Tyre operates approximately 12 manufacturing facilities, 9 in India and 3 in Mexico.
The company is steadily improving its financial performance. During the last 12 years, its sales turnover has more than doubled from Rs 6,924 crore in fiscal 2013 to Rs 15,002 crore in fiscal 2024, with operating profit more than trebling from Rs 618 crore to Rs 2,091 crore and the profit at net level shooting up more than four times from Rs 203 crore to Rs 806 crore. The company's financial position is very strong, with reserves at end of March 2024 standing at Rs 4,435 crore - over 86 times its equity capital of Rs 54 crore.
Established in 1958, CEAT stands as one of India's top tyre brands under the flagship company of the RPG group (Harsh Goenka faction). It provides a wide range of tyres, tubes and flaps for a wide range of vehicles, including cars, scooters, bikes, passenger vehicles (PVs), light commercial vehicles (LCVs), buses, trucks, tractors, two-wheelers and three-wheelers. The company caters to popular models such as Maruti Alto, Wagon R, Honda Shine, Swift, Dzire, Hero Splendor, Passion, Activa, Suzuki Access and TVS Jupiter. Through its e-commerce website, customers can opt for doorstep tyre delivery, fitment at home or pick-up from an authorised store. CEAT runs factories in Nashik, Mumbai, Halol and Ambernath, along with other cities across India. Furthermore, it exports its products to the US, Bangladesh, Sri Lanka and the Netherlands.
The company is doing extremely well on the financial front. During the last 12 years, its sales turnover has almost trebled from Rs 4992 crore in fiscal year 2013 to Rs 11,943 crore in fiscal 2024, with operating profit surging almost four times from Rs 454 crore to Rs 1,653 crore and the profit at net level shooting up more than five times from Rs 120 crore to Rs 635 crore. The company's financial position is very strong, with reserves at the end of March 2024 standing at Rs 4,002 crore, over 100 times its equity capital of Rs 40 crore.
April 15, 2025 - First Issue
Industry Review
Want to Subscribe?
Read Corporate India and add to your Business Intelligence
Unlock Unlimited Access
Lighter Vein
Popular Stories
Archives